Underlying Technologies – Metamaterials & Origami
This section introduces the core technologies behind Nature Architects’ design approach—metamaterials and origami—used to control physical properties through structural design.
Form-Finding Technology
To discover structures that appropriately control physical properties, Nature Architects is developing computational form-finding technologies.
By integrating a wide range of techniques—from geometry processing and numerical computation to optimization and machine learning—and combining them with our proprietary software, we enable the creation of new ideas grounded in simulation-driven design.
Solution Use Cases
For more details or information on unpublished case studies, please contact us.
Design Utilizing Additive Manufacturing
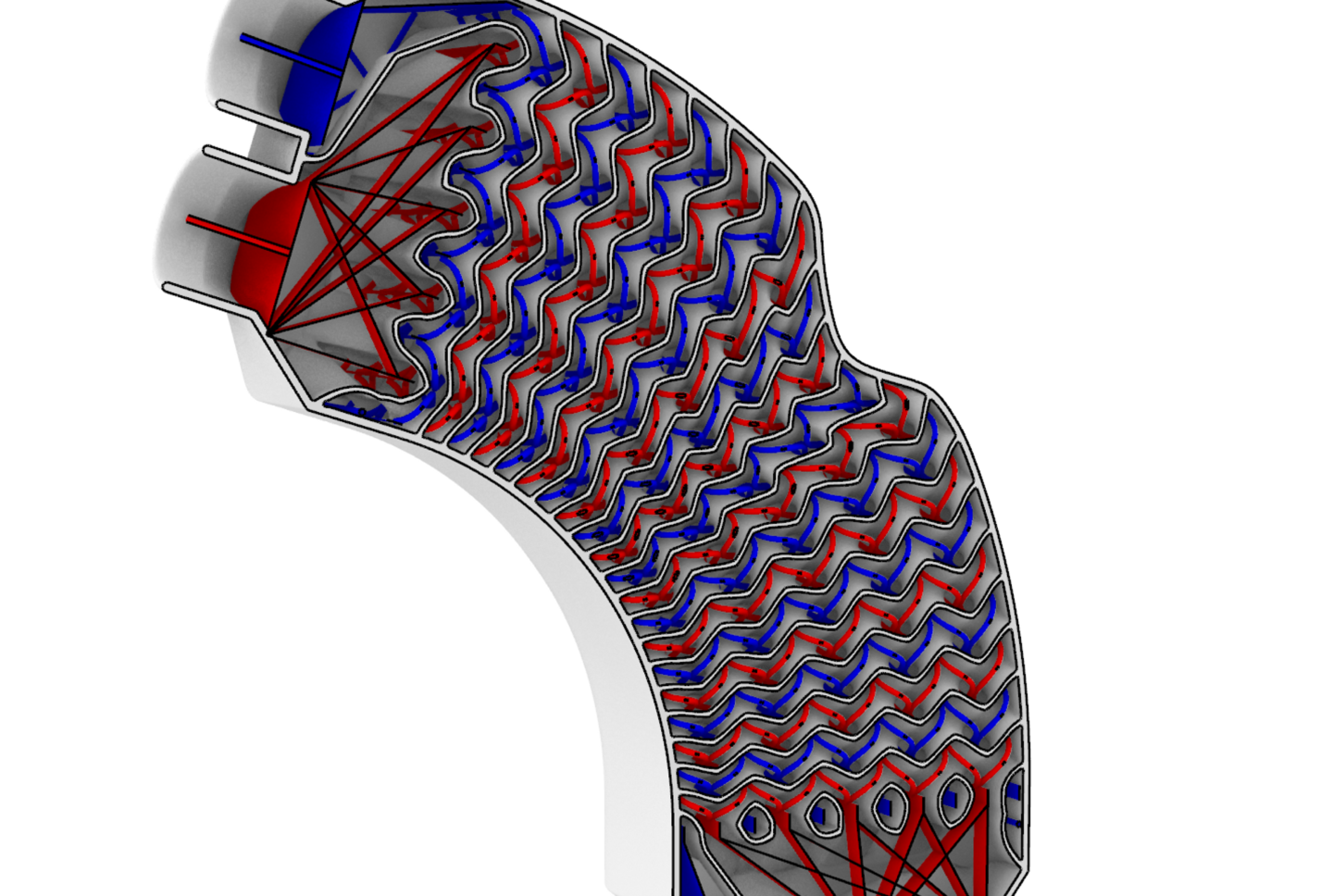
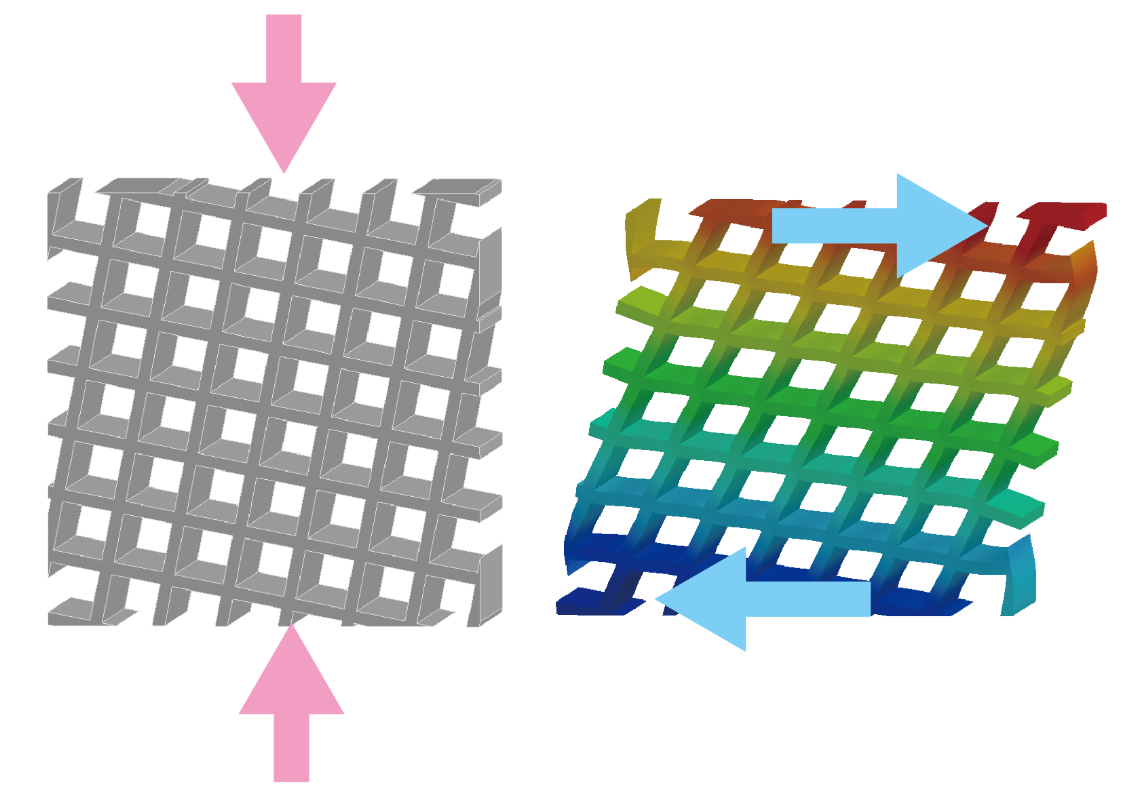
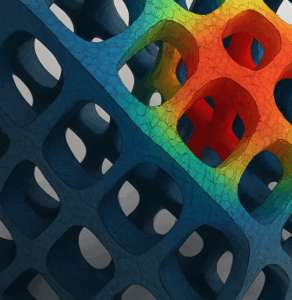